The packaging of pharmaceutical products is a crucial aspect of the industry. It serves not only as a protective barrier for the product, but also as a means of communication between the releaser and the consumer. The releaser, a pharmaceutical laboratory, must ensure the existence of an appropriate pharmacovigilance system that allows him to assume his responsibilities and obligations in relation to the pharmaceutical specialties he markets and ensure the adoption of appropriate measures when necessary.
Risks and consequences
One of the most important components of pharmaceutical packaging is the leaflet, also known as the patient information leaflet (PIL), which provides information about the product, including its intended use, side effects, and usage instructions.
To check the content of a leaflet thoroughly is critical, as even a small typo, missing text, or added text can have significant consequences for the patient and the releaser.
Why?
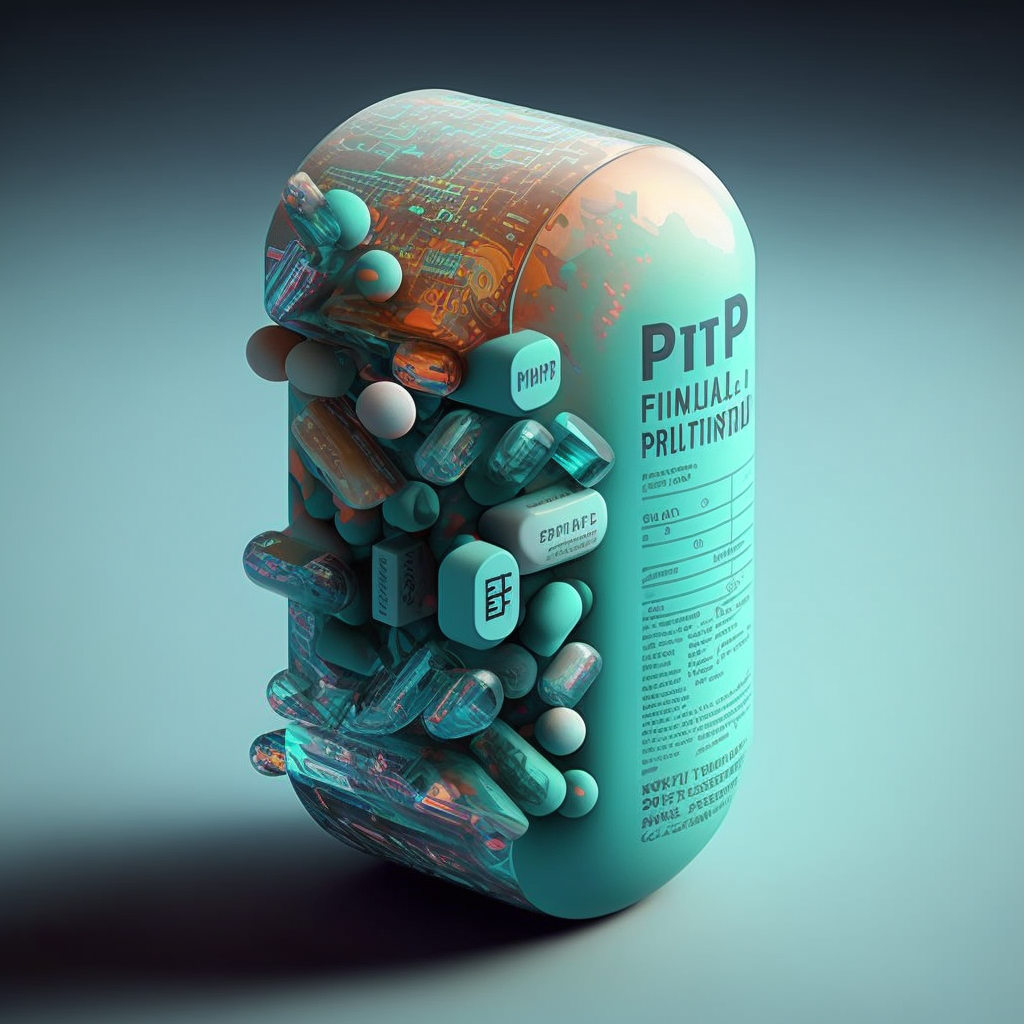
It is important to avoid errors in the leaflet because they can result in medication errors. For example, if a typo results in the incorrect dosage instructions being printed on the leaflet, the patient may take too much or too little of the medication, which can have serious consequences for their health. Similarly, if important information about side effects is missing or incorrect, the patient may not be fully aware of the risks associated with taking the medication. Believe me, there are side effects which patient and relatives should be fully aware from small possible irritations to a tendency to gambling, side effect that is only revealed after clinical trials for obvious reasons.
Deviation in the leaflet can also result in recalls and legal issues for the releaser. A recall is a costly and time-consuming process, as it requires to retrieve all the affected products from the market and replace them with new, corrected versions. In some cases, the recall may result in significant financial losses, as well as a damaged reputation and loss of trust from consumers.
As a designer and knowing the sensitivity of this situation, the corresponding procedure, quality documents and relevant tools are essential. Just thinking about the lack of an appropriate software 15 years ago makes me dizzy.
How to avoid mistakes
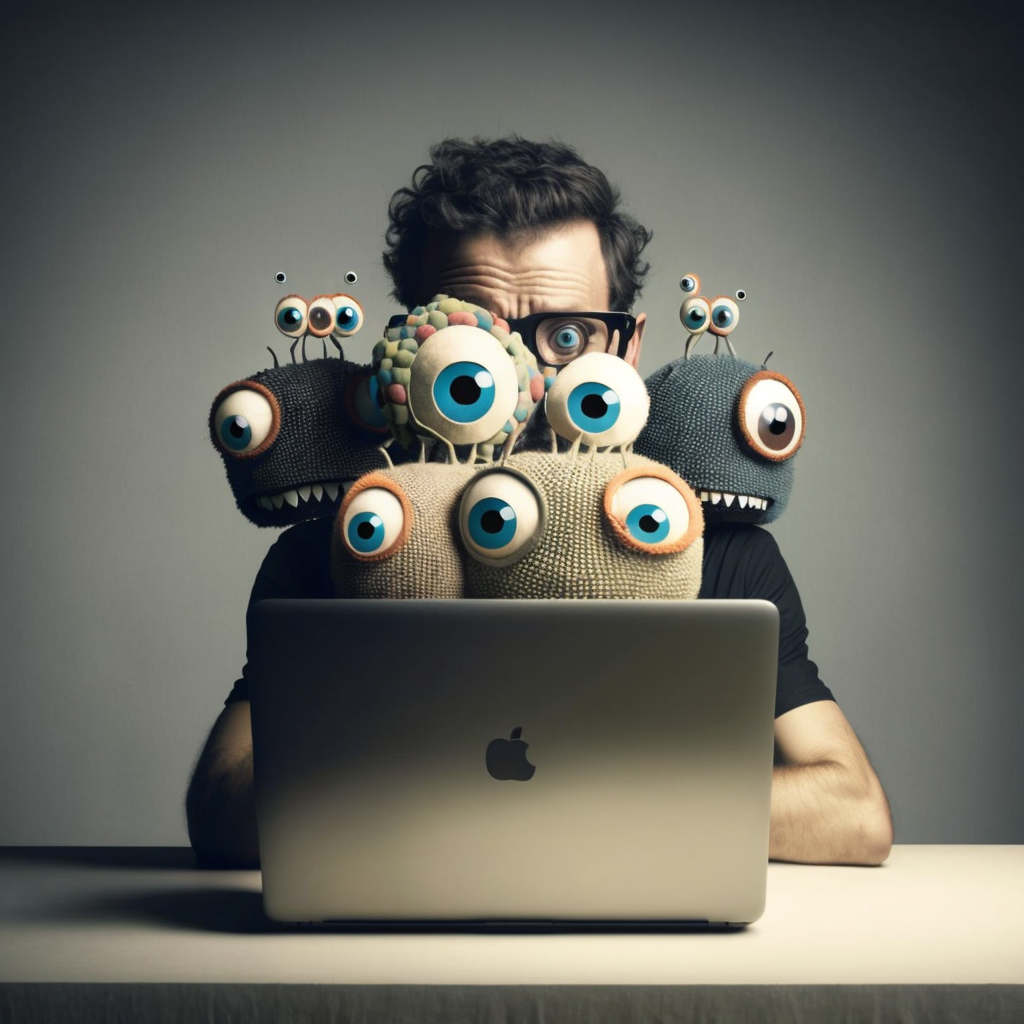
In order to avoid errors in the leaflet, it is important to have a robust quality control process in place. This may involve multiple rounds of review and testing by different employees within the company, we call it four eyes principle. The process should also include a thorough review of the final product before it is released to the market, in order to catch any last-minute changes or mistakes.
In conclusion, checking the content of a leaflet in the packaging of pharmaceutical products is a crucial step in ensuring patient safety and avoiding costly recalls and damage to brand image. By having a robust quality control process in place, releasers can avoid errors and ensure that the information provided in the leaflet is accurate and up-to-date. Patients can also play a role reporting any discrepancies to their healthcare provider. By working together, the industry and consumers can ensure that the information provided in the leaflet is accurate and that patients receive the best possible care.