La industria de los medicamentos genéricos es una parte integral del sistema de salud de todo el mundo. Sin embargo, existe un debate en curso sobre la verdad en la industria de los medicamentos genéricos. En este artículo, se discutirán las leyes que regulan el mercado de los medicamentos genéricos, así como la realidad química de los efectos beneficiosos y secundarios de estos medicamentos.
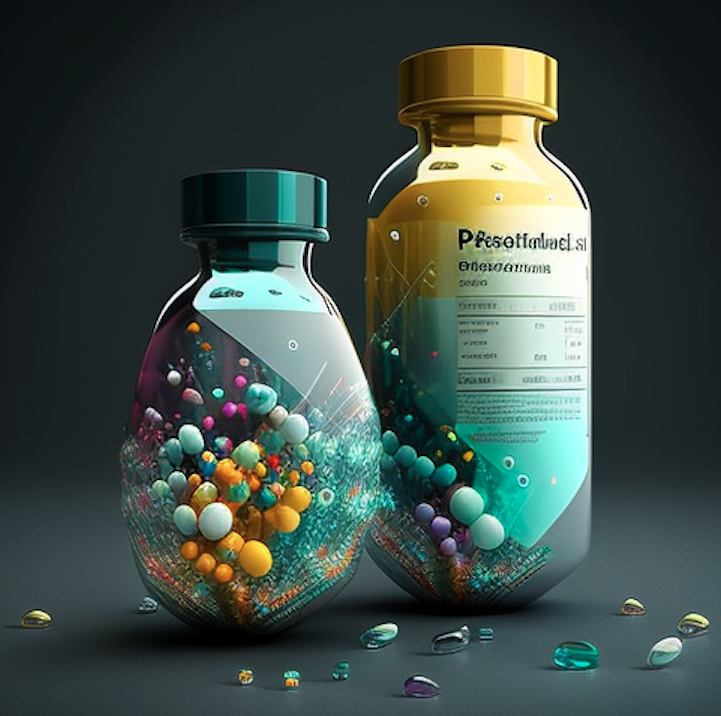
En primera instancia quien tiene cierta relación con la industria farmacéutica debería tenerlo claro pero lo cierto es que he oido a médicos cuestionarlo, si si, a médicos, en Europa en el siglo XXI. Bajo mi punto de vista este tipo de cosas, van de la mano con comentarios como que los aviones de una compañía de bajo coste son inseguros, el gran argumento es que supuestamente no pasan los mismos controles de seguridad en los aeropuertos. Ni voy a entrar en quien siembra este tipo de bulos por llamarlo de una manera menos hiriente, a los efectos da igual, es una cuestión de dejadez e ignorancia porque todos tenemos internet y con una búsqueda sobre la ley o entidad reguladora la duda queda resuelta.
Dicho esto y retomando el tema de los genéricos y centrándome en Europa, la ley cambió en 2004 donde desaparece la obligación de que el medicamento de referencia deba estar comercializado en el estado miembro en el que se pretende comercializar el medicamento genérico y se fija un único período de protección administrativa de los datos relativos al medicamento de referencia de 8 años aunque no podrán comercializarse hasta transcurridos los 10 años desde la fecha de autorización inicial del medicamento de referencia. Es decir, un laboratorio tiene 10 años para amortizar y rentabilizar un nuevo fármaco.
Leyes que regulan el mercado de los medicamentos genéricos
En Europa, la Agencia Europea de Medicamentos (EMA, por sus siglas en inglés) es la agencia responsable de la aprobación y regulación de los medicamentos, incluidos los medicamentos genéricos. La EMA requiere que los medicamentos genéricos sean bioequivalentes al medicamento de marca y cumplan con los mismos estándares de calidad, fuerza y pureza, es decir que contiene los mismos ingredientes activos y se absorbe de la misma manera en el cuerpo.
En los Estados Unidos, la FDA es la agencia federal responsable de la aprobación y regulación de los medicamentos con los mismos criterios de la EMA.
En ambos casos, la aprobación de un medicamento genérico requiere pruebas rigurosas y rigurosos estándares de seguridad y eficacia. Aunque algunos críticos argumentan que los medicamentos genéricos no son tan efectivos como los medicamentos de marca, los estudios han demostrado consistentemente que los medicamentos genéricos son igual de efectivos que los medicamentos de marca.
Realidad química de los efectos beneficiosos y secundarios de los medicamentos genéricos
La realidad química de los efectos beneficiosos de los medicamentos genéricos es la misma que la de los medicamentos de marca. Los medicamentos genéricos contienen los mismos ingredientes activos que los medicamentos de marca y, por lo tanto, tienen los mismos efectos beneficiosos. Sin embargo, los medicamentos genéricos pueden contener diferentes excipientes, que son los ingredientes inactivos que se utilizan para dar forma a la píldora, mejorar la absorción o el sabor, o para ayudar a preservar el medicamento. Estos excipientes pueden variar entre los medicamentos genéricos y de marca, pero no afectan la eficacia del medicamento. A veces esta parte es la que los escépticos toman como bandera para justificar lo incuestionable.
Por otro lado, los efectos secundarios de los medicamentos genéricos pueden ser diferentes de los efectos secundarios de los medicamentos de marca. Esto se debe a que algunos de los excipientes utilizados en los medicamentos genéricos pueden afectar la absorción y la metabolización del medicamento en el cuerpo, lo que puede afectar la probabilidad de experimentar efectos secundarios.
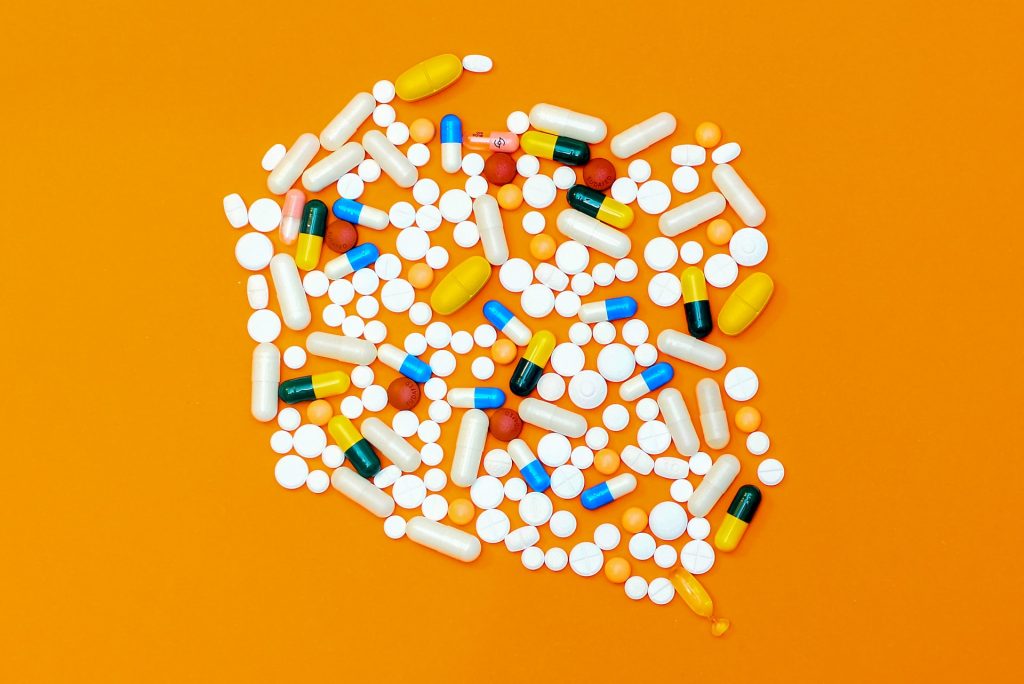
Para cerrar con un ejemplo, el ácido acetilsalicílico o AAS, conocido popularmente como aspirina, nombre de una marca que pasó al uso común, fue creada por Bayer en 1897, el siglo pasado ni más ni menos, es decir, el ácido acetilsalicílico es exactamente igual en todos y cada uno de los laboratorios que se produce en todo el mundo, ¿queda alguna duda al respecto?.
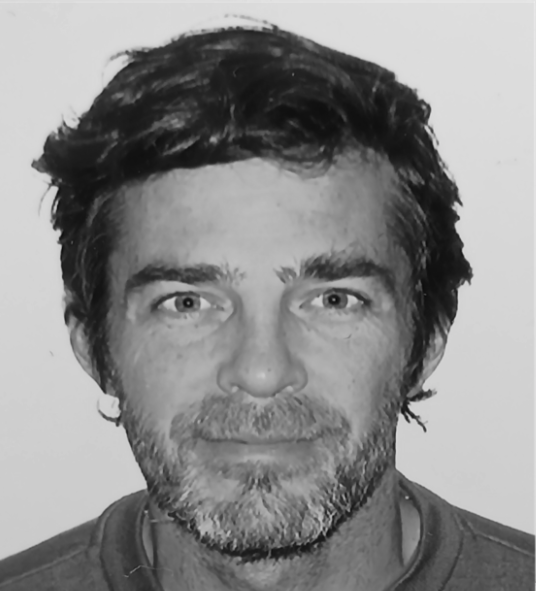
Artwork Manager